CASE STUDY: Walking surfaces for natural gas extraction site
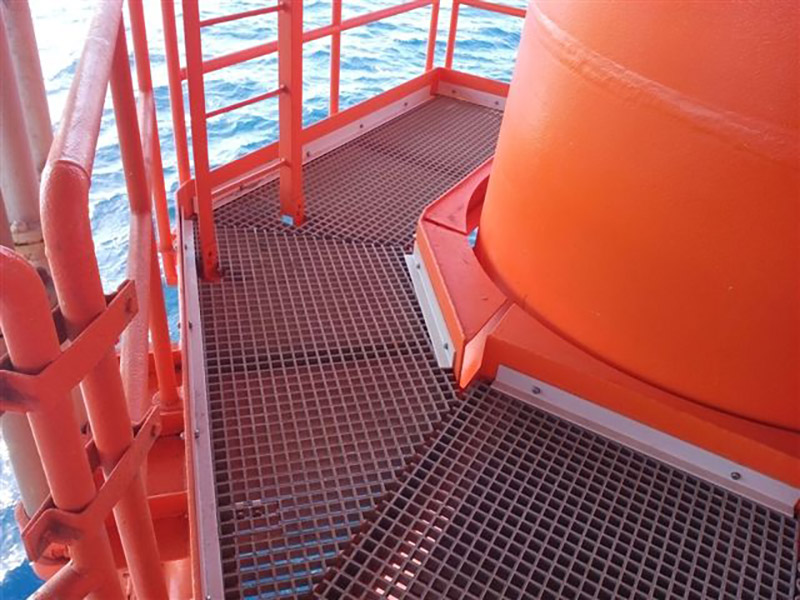
The Together for Tomorrow network’s case studies also include the project on a natural gas extraction station off the Mediterranean coast of North Africa, which was developed in two phases.
Phase 1: the client was looking for an alternative to traditional metal gratings, which need constant maintenance and had to be frequently replaced, due to their low resistance to the environmental aggression of sea water. Brackish environment causes rust formation and a consequent rapid deterioration of metal gratings, making walking surfaces extremely dangerous.
In order to meet such requirement, the company of the network M.M. supplied 450m² FRP gratings and FRP angle brackets (Fiberglass Reinforced Polymers). FRP products are ideal for applications in direct contact with brackish water because no salt deposit is left on the material (as evidenced by the test carried out by M.M. in collaboration with the University of Rome Tor Vergata). Thus, corrosion problems and maintenance costs have been removed, while enhancing safety. All walking surfaces were made with non-slip finishings.
Phase 2: the client needed to replace the chlorination tank of the platform’s water treatment plant. The tank, made of metal, was heavily damaged, both by the chemicals contained and the brackish environment.
The intervention was conditioned by several critical issues, such as the choice of the type of resin suitable for the use of the tank, as well as the design of the internal gates and the walkable cover.
Furthermore, due to the overall dimensions in the installation area, it was necessary to produce the tank in two halves to be positioned one at a time and connected to each other in a following stage of the installation.
After the inspection by the technicians of Company Carbon Compositi, who verified all the needs and limits of the work in accordance with EN 13121.3 Standard the synergy between the technical crews of Carbon Compositi and M.M. made it possible to design a tank, subsequently built by Lamar Udine, capable of a full compliance with the needs of the client.
The work environment required the use of a self-extinguishing vinylester resin with the addition of special fillers, while the external liner was made with a pure vinylester resin gel coat provided with ultraviolet absorbent, in order to adequately resist to the exposure to UV rays.
The two parts of the tank were equipped with a flanged joint along the entire coupling length. During the installation phase, the joint was finished internally in order to ensure the hydraulic seal of the tank.
Once the tank was installed, several flanged nozzles were installed on its side walls in order to connect it to the system lines. All the installation activities were performed by Carbon Compositi, while M.M., as Main Contractor,was in charge of the complete management of the project.